Popular Products
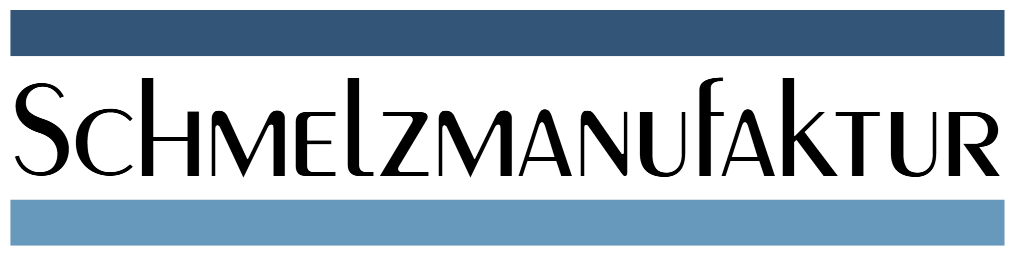
Welcome to the online store of Schmelzmanufaktur
We offer plastic parts in FDM manufacturing technology. Different materials can be used, depending on the requirements.
In 3D printing there are many different materials with very different properties for several years.
Every year, improved or new ( bio) plastics are added, which again open up new possibilities.
Which materials do we use?
Bio plastics
There are various plastics that consist of 100% renewable raw materials and are biodegradable according to DIN EN ISO 14855.In addition, the raw material has food approval (FDA).
The heat resistance and resilience can keep up with the standard plastic types such as PETG and ABS and even surpasses them in certain areas.
The surface is more of a matte sheen. The component does not generate further plastic waste at the end of its service life, but is biodegradable.
Nylon
Components made of nylon can withstand extremely high thermal and mechanical stresses. The layer adhesion is also much greater here compared to the biocomposite.
However, nylon can only be used for dry environments, as nylon is hygroscopic and absorbs water.
TPU
TPU with a Shore hardness of D58 can be used for flexible components. The major advantage is its impact resistance. This material does not splinter or break when force is applied. It also has extremely high layer adhesion.
Depending on the wall thickness and degree of filling of the component, the flexibility can be varied. A cube with edge length 10mm and high infill could not be visibly deformed by hand.
Polycarbonate
Components made of polycarbonate can withstand higher thermal and mechanical loads than the biocomposite. The layer adhesion is also greater than that of the biocomposite.
Polycarbonate has a rather glossy surface and is food safe.